
Curso Online de Operador e Programador de Extrusora Injetora
O curso de Operador e programador de extrusora injetora tem a intenção de promover o aprimoramento dos profissionais da área no que tange...
Continue lendo
- Aqui você não precisa esperar o prazo de compensação do pagamento para começar a aprender. Inicie agora mesmo e pague depois.
- O curso é todo feito pela Internet. Assim você pode acessar de qualquer lugar, 24 horas por dia, 7 dias por semana.
- Se não gostar do curso você tem 7 dias para solicitar (através da pagina de contato) o cancelamento ou a devolução do valor investido.*
- Adquira certificado ou apostila impressos e receba em casa. Os certificados são impressos em papel de gramatura diferente e com marca d'água.**
** Material opcional, vendido separadamente.
Modelo de certificados (imagem ilustrativa):
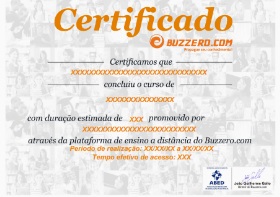
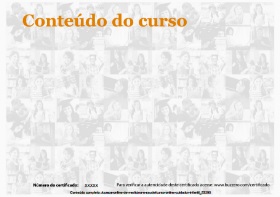
-
Operador e Programador de Extrusora Injetora
-
SEJA BEM VINDO
AO CURSO
Operador e Programador de Extrusora Injetora
-
O curso de Operador e programador de extrusora injetora tem a intenção de promover o aprimoramento dos profissionais da área no que tange seus principais conteúdos, tais como: máquinas sopradoras, processo de sopro, segurança na operação com sopradoras, operação de extrusoras para filme tubular, máquinas extrusoras para filmes, matrizes.
-
OPERAÇÃO DE EXTRUSORAS POR SOPRO PARA PLÁSTICOS
O processo de transformação de plásticos por sopro atualmente ocupa uma posição estratégica no segmento de embalagens para produtos das mais diversas áreas de consumo, alguns exemplos comumente percebidos são o setor alimentício, limpeza, derivados de petróleo e cosméticos. Os produtos soprados carregam consigo vantagens em relação às embalagens convencionais, como aumento da resistência a quedas, aliado ao baixo custo que pode proporcionar no produto final frente a alta produtividade e segurança que este método pode apresentar. Outros segmentos utilizam os benefícios disponibilizados por este processo que oportuniza vantagens ao público consumidor em geral, que é o acesso a bens que antes não atingiam as classes de menor poder aquisitivo
-
PARTES DA MÁQUINA O equipamento é um conjunto de componentes com funções específicas, os quais são relacionados a seguir. 3.1 Base É a estrutura onde se apóiam ou estão alojados todos os pontos da máquina. Sua forma varia conforme a disposição relativa dos elementos e seu tamanho podem ser formados por perfis de aço soldados ou chapas grossas dobradas e soldadas ou ainda ser executada em fundição. Deve-se ter cuidado de em sua execução e ou manutenção, prover-lhe suficiente rigidez para que não entre em ressonância com as freqüências de vibração que possam ser geradas no movimento de outras partes. (SERVIÇO NACIONAL DE APRENDIZAGEM INDUSTRIAL, 2002). 3.2 Funil de alimentação É o depósito de material granulado para ser processado. Sua capacidade depende do tamanho de máquina sopradora. Deve ser mantido sempre tapado para evitar que impurezas contaminem o material granulado. 3.3 Cilindro de aquecimento Recebe o material plástico no seu interior e transmite-lhe calor promovendo a plastificação. (SENAI-RS, 2002)
-
Rosca plastificadora A função da rosca plastificadora na máquina de sopro, consiste em primeira etapa de transportar, fundir e homogeneizar o material plástico, através de movimento rotativo. Devido as propriedades intrínsecas de cada material plástico, tais como: dureza superficial dos grânulos, temperatura de fusão, coeficiente de cisalhamento, viscosidade do material fundido, e outras, faz-se necessário desenvolver diferentes construções de rosca para cada termoplástico. Na prática, porém o que se nota são roscas padrões que procuram atender grupos de materiais com comportamento reológicos parecidos. Geometricamente ela é dividida em três zonas distintas (FIG. 2): A - Zona de Alimentação - tem como função transportar os grânulos sólidos para a zona de compressão ou plastificação. Nesta zona o núcleo da rosca tem o menor diâmetro, se mantendo constante. Esta parte da rosca deve assegurar uma pressão de alimentação e pré-aquecer o material. B - Zona de Compressão - é a zona onde se inicia a plastificação, devido ao aumento constante do núcleo da rosca, que irá comprimir e cisalhar o material plástico. A diminuição do volume disponível entre os filetes da rosca, além de fornecer compressão e auxiliar a plastificação, tende a homogeneizar a massa que se funde, eliminando o ar inicialmente incluso entre os grânulos através do funil de alimentação. C- Zona de Dosagem -nesta zona têm filetes com profundidade rasa, isto porque o diâmetro do núcleo da rosca vem crescendo atingindo aqui sua maior dimensão e permanecendo constante. É na zona de dosagem que se completa a plastificação, e se faz a homogeneização máxima, definindo também o bombeamento da massa fundida para a câmara frontal. (SENAI-RS, 2002).
-
Bloco de Empuxe Em seu giro, a rosca exerce sobre o material uma determinada ação que se traduz no bombeamento suficiente para atravessar o cabeçote ou matriz de extrusão. Como conseqüência desta ação de empurrar o material a rosca recebe um esforço de empuxe ou reação até parte posterior, que deve ser contida de alguma forma. O conjunto de peças mecânicas destinadas a transmitir a rosca sua rotação, suportando também seu empuxe axial até a parte posterior, denomina-se bloco de empuxe. (SENAI-RS, 2002).
-
Redutores As velocidades de rotação das roscas podem tomar valores entre 0 e 230 rpm, o que equivale a velocidades periféricas de até 50 m/min. Como as máquinas de impulsão são em geral motores elétricos trifásicos assíncronos, e giram em torno de 1200 a 2400 rpm, deve-se transmitir a força motriz através de uma redução de velocidade e prover uma transmissão do motor ao redutor e deste ao fuso extrusor. 3.7 Grupo Motriz ou Variador de Velocidade “Embora a rosca deva girar a uma velocidade constante quando a máquina produzir em uma determinada forma, esta velocidade deve ser variada durante a otimização do processo de produção. Daí o uso de variadores de velocidade.” (SENAI-RS, 2002). 3.8 Painel Elétrico O painel elétrico do equipamento deverá ser revisado a cada 6 meses, com reaperto dos parafusos dos bornes de ligação, bem como todos os instrumentos de medição e leitura que houver. 3.9 Cabeçote O cabeçote é uma continuação da extrusora [(FIG. 3)]. Quando o polímero fundido entra no cabeçote, ele se divide no mandril, porém ao sair do corpo da matriz, o fluxo já deve ter sido unido e sem nenhuma área fraca para que uma pré-forma bastante uniforme se torne uma peça soprada bem acabada e sem nenhuma imperfeição. O projeto do cabeçote exige sempre aerodinâmica nas passagens, por isso são necessários usinagens e polimento superficial para impedir pontos mortos, o que provocaria estagnação do polímero e consequentemente sua degradação térmica. (SENAI-RS, 2002).
-
Cabeçotes de entrega transversal com núcleo fixo em sua parte superior, onde a massa flui radialmente; Cabeçote acumulador; Cabeçote com êmbolo acumulador. (SENAI-RS, 2002). 4 PROCESSO DE SOPRO E EQUIPAMENTOS Moldagem por sopro é um processo para produzir artigos ocos fechados. Este processo foi desenvolvido originalmente para a indústria de vidro, mas, hoje em dia, é utilizado extensamente na indústria dos plásticos, porém limitado a materiais termoplásticos como, por exemplo: Polietileno , PVC, etc. (INSTITUTO AVANÇADO DO PLÁSTICO, [20--?]). “Processo em geral utilizado na obtenção de peças ocas através da insuflação de ar no interior do molde, de forma a permitir a expansão da massa plástica, até a obtenção da forma desejada. Aplicável geralmente à fabricação de frascos a partir de termoplásticos.” (SILVA JR; ALEX, [20--]). A técnica de moldagem por sopro pode ser dividida em três principais classes: moldagem por extrusão-sopro, que usa basicamente um parison suspenso; moldagem por injeção-sopro, que usa um parison suportado por um pino metálico; uma terceira classe que inclui a moldagem por estiramento-sopro (stretch-blow moulding) e a moldagem por coextrusão-sopro. (SENAI-RS, 2002). O processo de extrusão-sopro pode, ainda, ser subdividido em dois processos: contínuo e intermitente. A extrusão-sopro intermitente também pode ser subdividida em: extrusão com rosca reciprocante, extrusão com ajuda de pistão e extrusão com uso de cabeçote acumulador. A moldagem por estiramentosopro e coextrusão-sopro são na verdade, uma evolução da moldagem por extrusão-sopro. (SENAI-RS, 2002).
-
Descrição do processo A unidade de produção para um processo de moldagem por sopro é composta dos seguintes componentes: A máquina de produção utilizada para produzir plástico fundido (uma extrusora ou uma máquina de injeção é utilizada para produzir plástico fundido), O sistema para formar o parison, O molde de sopro (ou moldes de sopro). Em ambos os principais processos o primeiro passo envolve a produção de uma mangueira. Esta mangueira é conhecida no ramo em geral como parison (o termo foi emprestado da indústria de vidro). Na moldagem por extrusão (EBM - extrusion blow molding), o parison é produzido por extrusão, e na moldagem por injeção (IBM - injection blow molding) o parison que também conhecido como pré-forma, é produzido por injeção. Como o período de refrigeração é a parte mais demorada do ciclo de sopro, será necessário retirar o parison do cabeçote (ou cabeçotes), ou desviar o fluxo de material de um molde para outro, com a finalidade de manter a rosca em movimento contínuo. Para exigências de alta produção, os moldes podem ser instalados numa cinta giratória rápida, ou numa roda (carrosséis horizontais ou verticais). Porém, é mais comum os moldes serem instalados em sistemas de fechamento e sopro (estações de sopro ou carros), que estão dispostas por
-
baixo ou ao lado da extrusora. O conjunto de moldes pode ser utilizado para transportar o parison na configuração normal, por exemplo, montado num braço basculante, ou podem ser usados alicates para deslocar o parison para o molde. (WHELAN, 1999). É um processo predominantemente contínuo de transformação de plásticos onde a unidade de plastificação recebe a matéria-prima ainda no estado sólido em forma de grãos, moído ou em pó. Este processo transporta o material a ser extrusado, processando-o através da ação de calor das resistências e fricção mecânica da rosca de plastificação e cilindro. Após friccionado, o material passa para o estado pastoso, sendo empurrado para a matriz que forma o parison (designação importada da indústria do vidro). Por parison entende-se um tubo plástico amolecido que é ‘abraçado’ pelo molde de sopro. Este (molde de sopro) utiliza-se, então, de uma agulha que insufla ar para o interior do molde, permitindo, assim, a expansão da massa plástica até os limites do molde de sopro. Após o resfriamento completo começam as operações de acabamento (rebarbagem, por exemplo) e o produto é extraído [(FIG. 4)]. (SENAI-RS, 2011). Muitas máquinas de sopro dependem de uma extrusora para produzir plástico fundido, já que uma extrusora de rosca única consegue produzir uma massa plastificada a temperaturas baixas com custo relativamente baixo. Aproximadamente 90% de todos os produtos moldados por sopro são feitos pelo processo EBM (moldagem por extrusão e sopro). (WHELAN, 1999). Independentemente do material processado, as temperaturas de plastificação devem ser mantidas as mais baixas possíveis para reduzir os tempos de refrigeração. Na moldagem por sopro o tempo de refrigeração, normalmente é a parte mais demorada do ciclo, por exemplo, até 80%. A extrusora também deve ser capaz de acomodar a adição de quantidades variáveis de aditivos, por exemplo, material recuperado, materiais para coloração, modificadores de impacto e estabilizadores. Quando a máquina não necessita produzir compostos, o projeto pode ser otimizado para processar material prémisturado, quer dizer, para alcançar a produção necessária em libras por hora (lbs/h) ou quilogramas por hora (kg/h) de uma massa plastificada uniformemente a baixas temperaturas. Na moldagem por sopro é vital manter a temperatura do fundido na margem mais baixa, porque com isso é possível aumentar a produção. (WHELAN, 1999).
Pagamento único

Cursos Relacionados
-
Programador de computador
A profissão de programador ou programadora está em alta no mercado e existe uma grande carência de profissionais capacitados , se você se...
R$ 49,904h
-
Operador de Máquinas e Equipamentos
Operador de Máquinas e Equipamentos Objetivos: Neste curso iremos abordar as técnicas de Operação, manutenção, direção e Prevenção Acid...
R$ 39,90170h
400+
-
Operador de Telemarketing
Olá seja bem-vindo ao curso de Operador Telemarketing aqui você vai aprender tudo o que é necessário para ingressar nessa área! Nosso cur...
R$ 24,904h
Encontre-nos no Facebook
Capítulos
- Operador e Programador de Extrusora Injetora
- OPERAÇÃO DE EXTRUSORAS POR SOPRO PARA PLÁSTICOS
- OPERAÇÃO DE EXTRUSORAS PARA FILME TUBULAR
- OPERAÇÃO DE EXTRUSORAS PARA GRANULAÇÃO
- SEGURANÇA NA OPERAÇÃO COM SOPRADORAS
- PROCESSO DE EXTRUSÃO DE FILME TUBULAR
- MÁQUINAS EXTRUSORAS PARA GRANULAÇÃO
- SEGURANÇA NA OPERAÇÃO COM INJETORAS
- OPERAÇÃO DE INJETORAS PARA PLÁSTICOS
- FUNDAMENTOS DE MATERIAIS PLÁSTICOS
- MÁQUINAS EXTRUSORAS PARA FILMES
- MÁQUINAS SOPRADORAS
- PROCESSO DE INJEÇÃO
- MÁQUINAS INJETORAS
- PROCESSO DE SOPRO
- referência
- AGRADECIMENTO